A blog filled with product announcements, customer stories, and best practices for vendors and distributors.
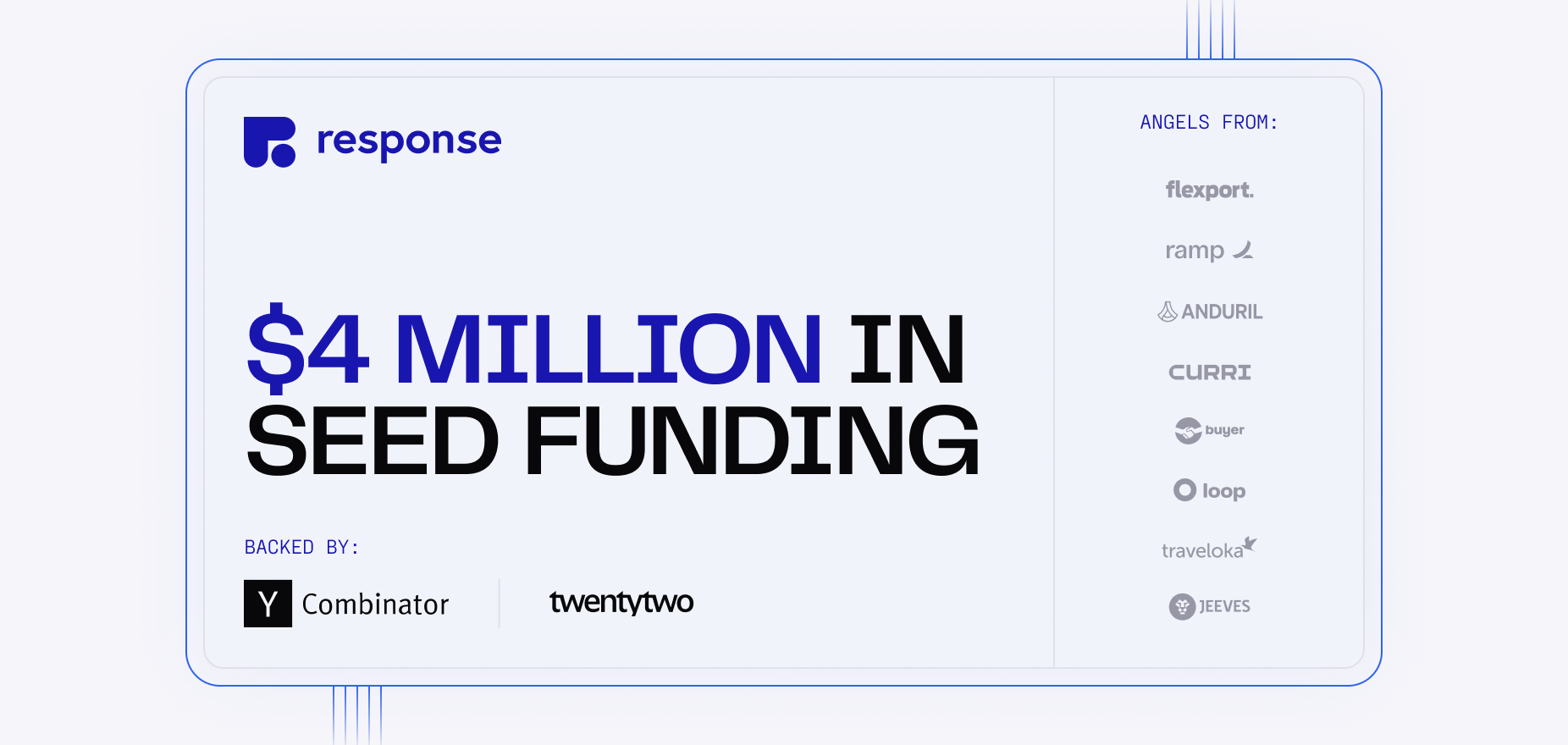
Response raises $4M seed funding to help companies take control of indirect spend
We’re thrilled to announce that Response has raised $4M in seed funding, with support from Y Combinator, Twenty Two Ventures, and strategic angel investors from Flexport, Anduril, Ramp, Scale AI, and more. With $4.3M in total funding to date, we’re doubling down on building proactive “spend insights” to monitor spending, uncover savings opportunities, and power workflows that automate the entire ordering process—from start to finish. Why indirect spend is a hidden profit killer Indirect spend—everyday business expenses like packaging, maintenance supplies, and office essentials—quietly eats away at company margins when left unmanaged. While it typically consumes 10-15% of revenue, many businesses rely on manual processes like spreadsheets and corporate cards to manage it. This lack of structure leads to: Lack of visibility: Teams don’t know who’s buying what, where, and at what price. Wasted money: Fragmented purchases weaken negotiating power, driving up costs. Wasted time: Disjointed workflows and approval processes keep employees stuck in low-value tasks. For too long, indirect spend has flown under the radar. We built Response to change that. The platform Unlike traditional procurement platforms, Response integrates with nearly 100 top industrial vendors for real-time pricing and direct ordering—without clunky “punchouts.” For vendors outside our network, purchase order management lets teams order globally while maintaining full control of spend. Admins gain simple yet powerful tools to set product and spending limits by department, location, or seniority. For their teams, it’s as easy as online shopping—with built-in guardrails to prevent overspending. What we’ve built so far: Real-time SKU-level visibility: Know exactly what’s being purchased, by whom, and at what cost. Purchase controls: Set spend limits, enforce pre-approved product lists, and streamline approval processes. Multi-vendor checkout: Purchase from nearly 100 top industrial vendors with 1-click integrations—no clunky "punchouts." Consolidate orders and manage POs seamlessly. Personalized storefronts: Control product access by department and location, ensuring teams buy what they need, when they need it, within budget. Results Our customers have achieved: Up to 91.6% faster ordering. No delays, no wasted time. Up to 13.2% cost savings. No waste, no overspending. As low as <1% rogue spend. No off-the-books purchases, no budget surprises. What our customers are saying: "Response has transformed our procurement process. The time savings alone make it worthwhile, but the real value lies in the visibility and control we now have over our spend. Our managers are more efficient, our accounting team is happier, and we're running a leaner operation overall." — Sterling Westfall, Head of Operations, Nimbl Fulfillment Companies like publicly traded eCommerce aggregator Aterian (NASDAQ: ATER) and logistics leader Warehouse Specialists Inc. (WSI) trust Response to take the guesswork out of indirect spend—and the results speak for themselves. If you want to see Response in action, watch our platform overview or book a demo. What's next? Our vision is to create the world’s first digital procurement officer—starting with indirect spend. Customers don’t need more software—they need real solutions. They want the busywork of ordering and the guesswork of negotiation off their plates, and that’s exactly where we come in. We’re doubling down on "spend insights" to continuously monitor spending and uncover savings, while developing workflows to automate the entire ordering process—from start to finish. Thank you A huge thank you to our customers, investors, and team for making this possible. The time to take control of unmanaged spend is now. Don’t miss out. Keivan, Kais, and the Response team Ready to stop the waste, stay on budget, and start saving? Book a demo.
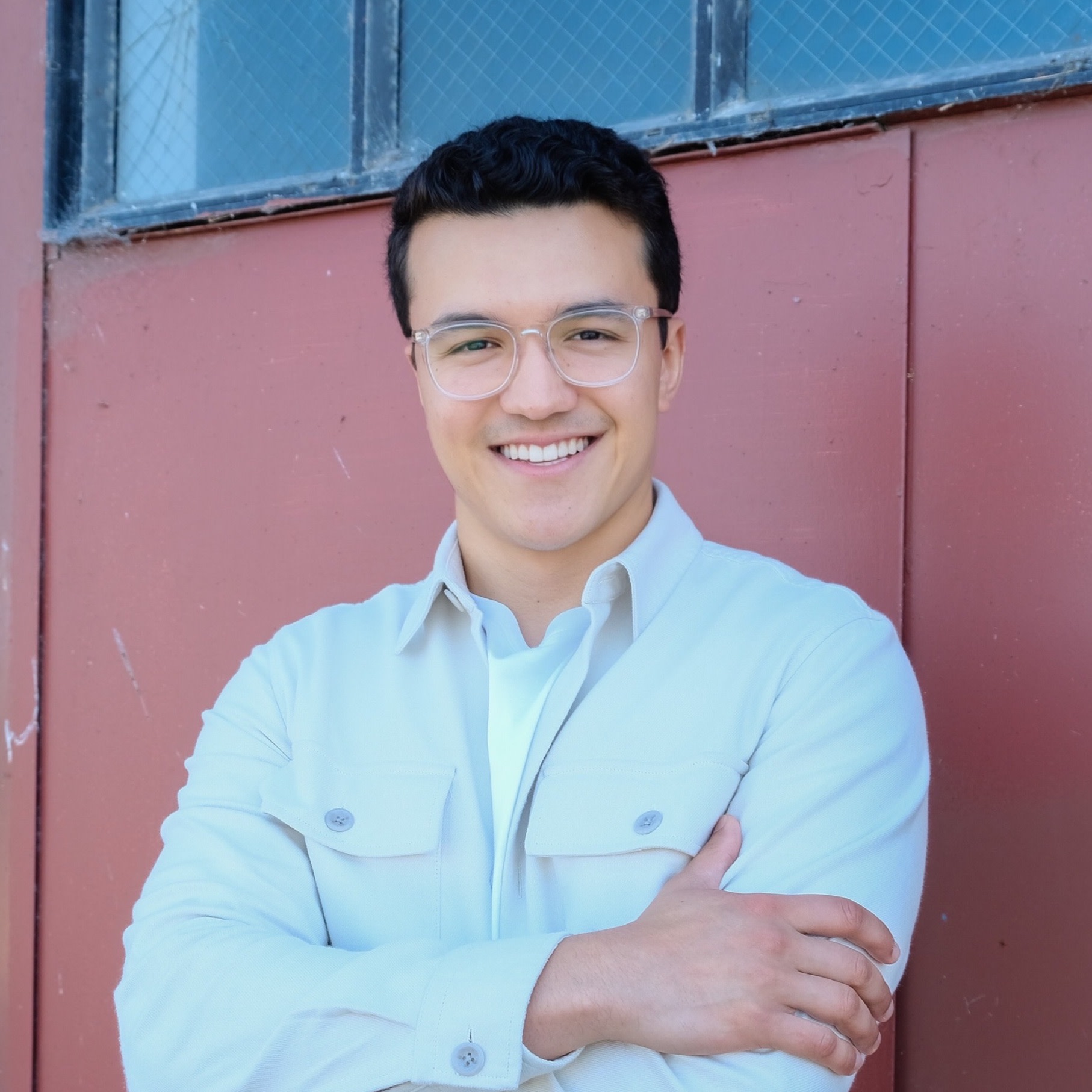
Categories
Previous Articles
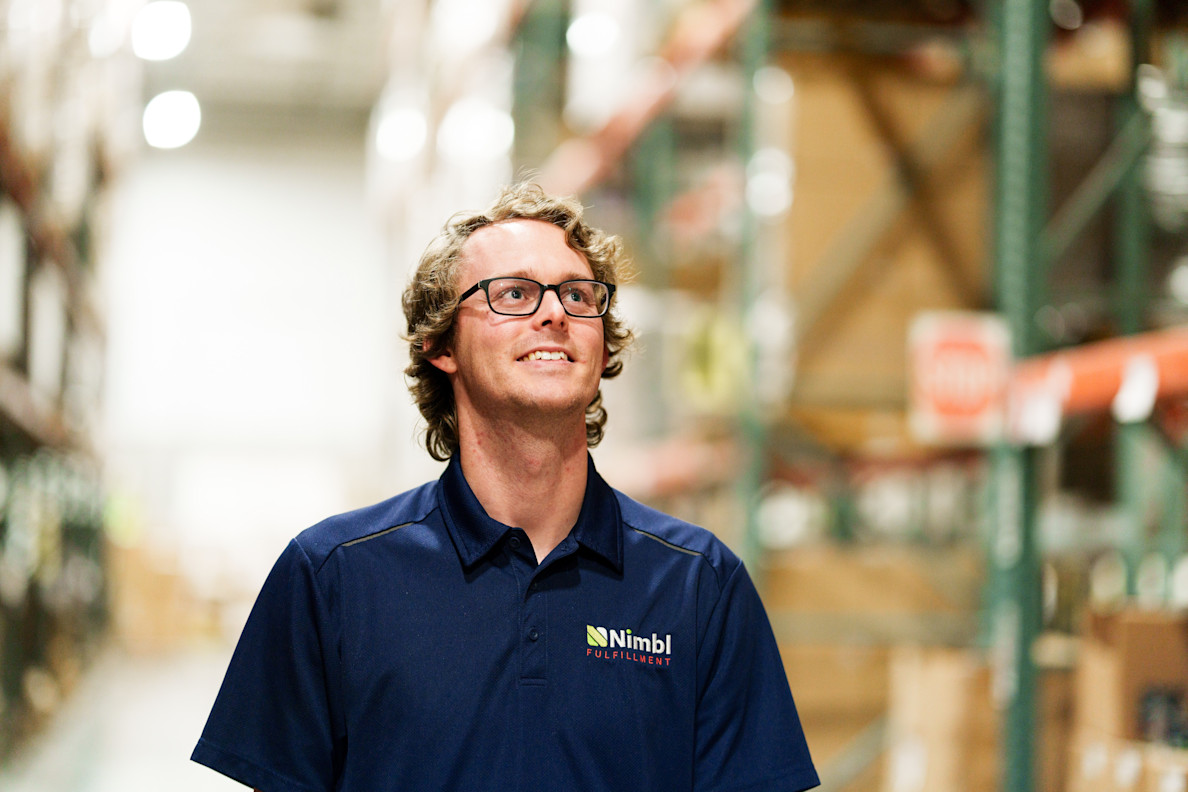
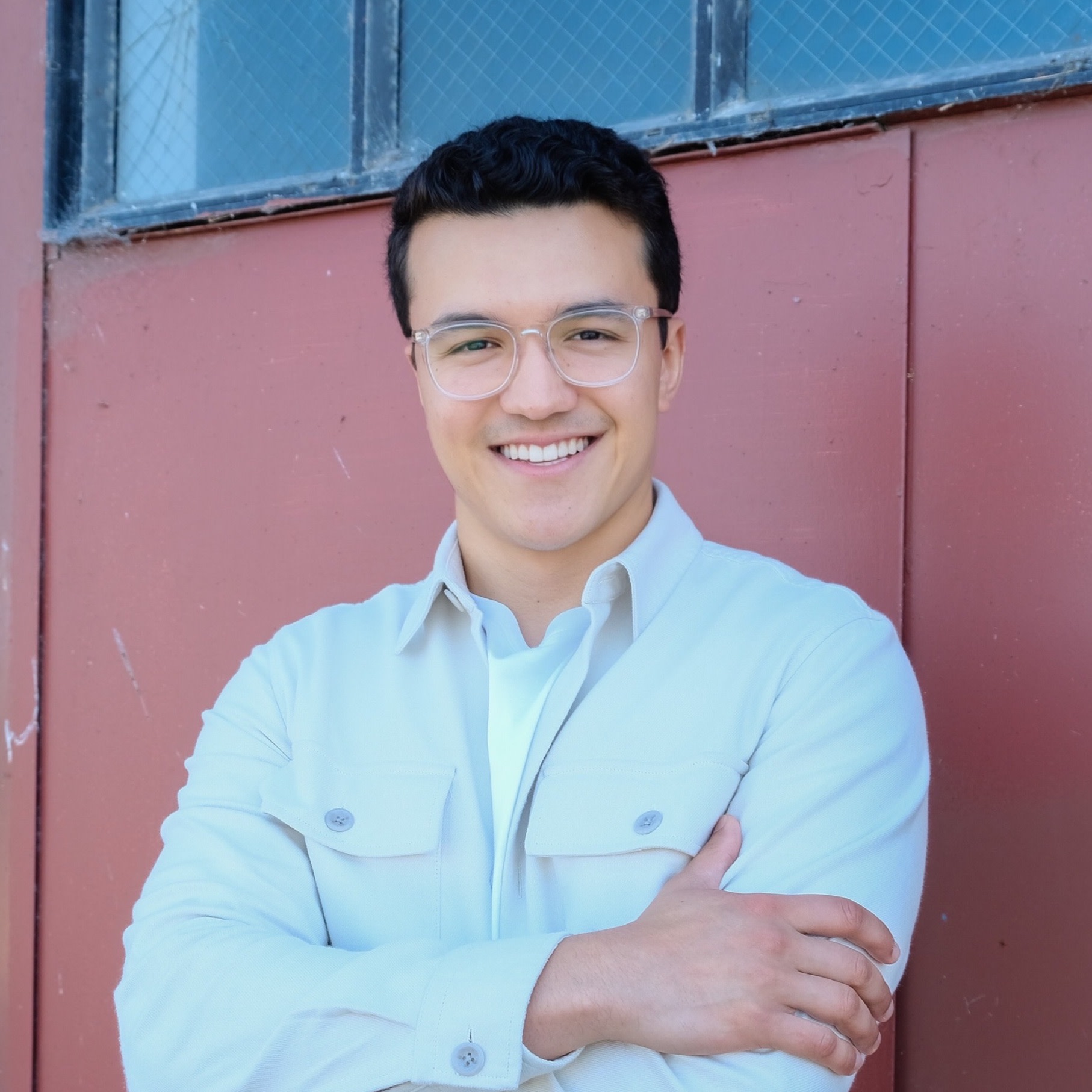
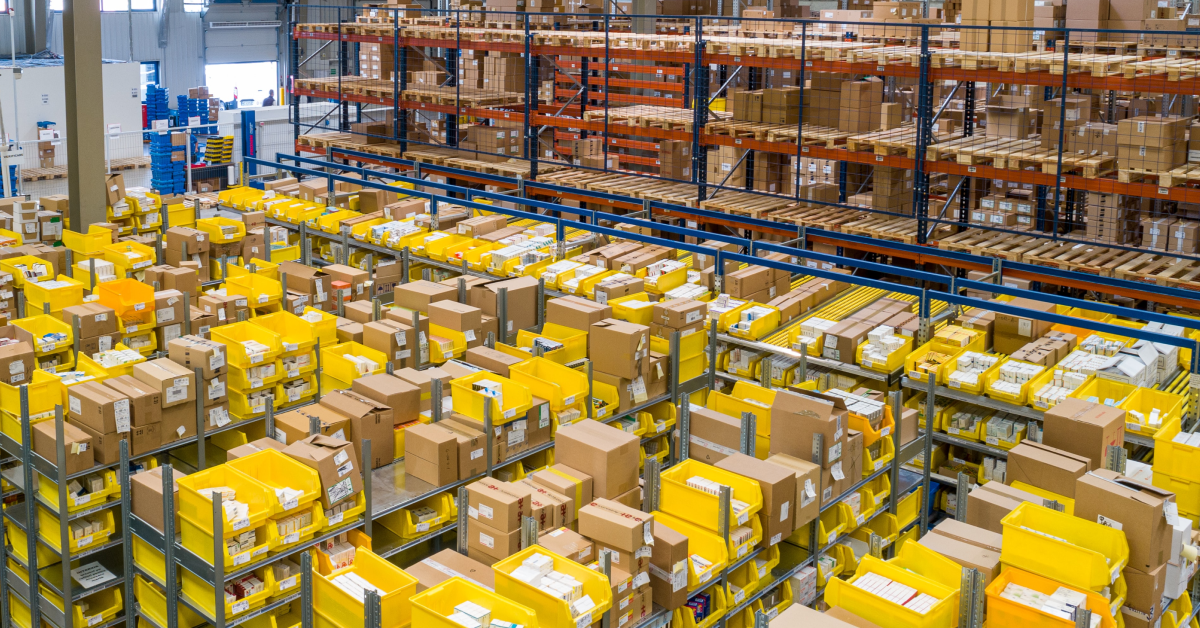
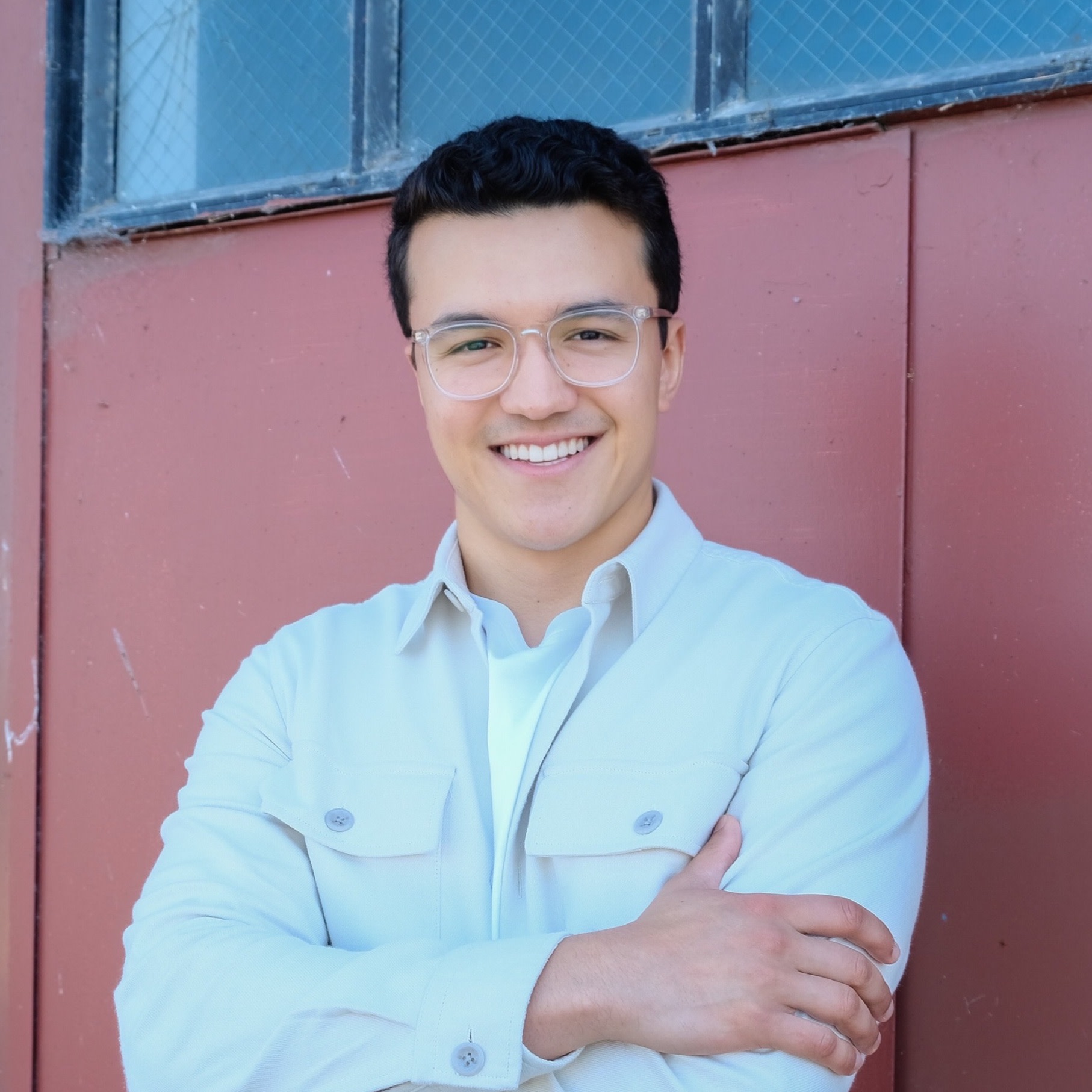
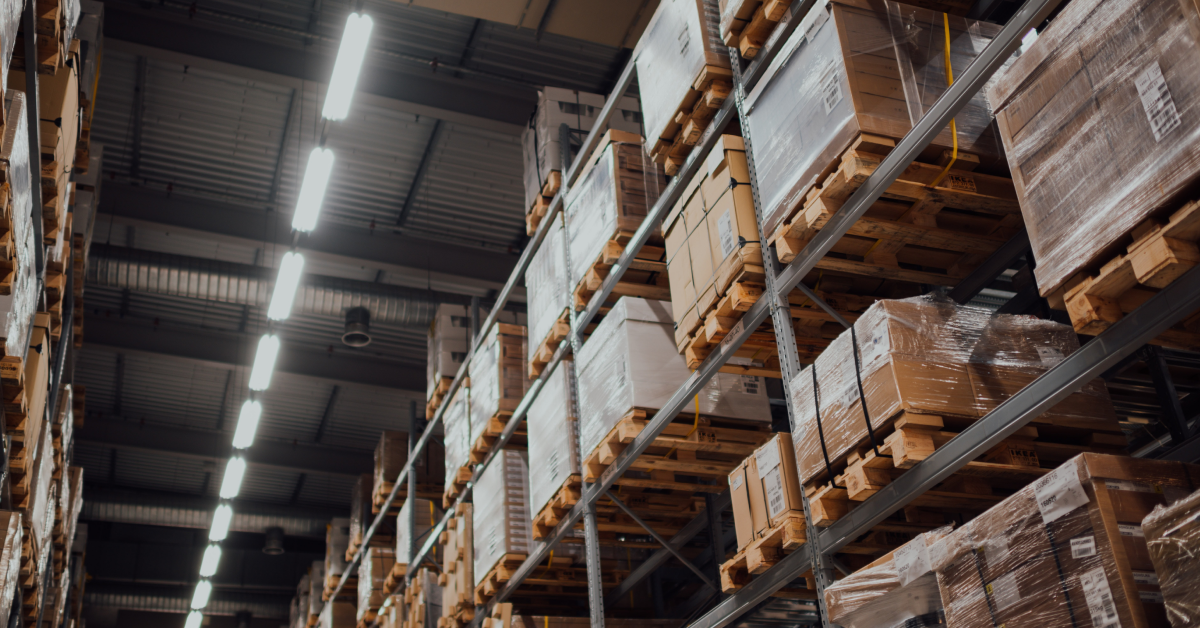
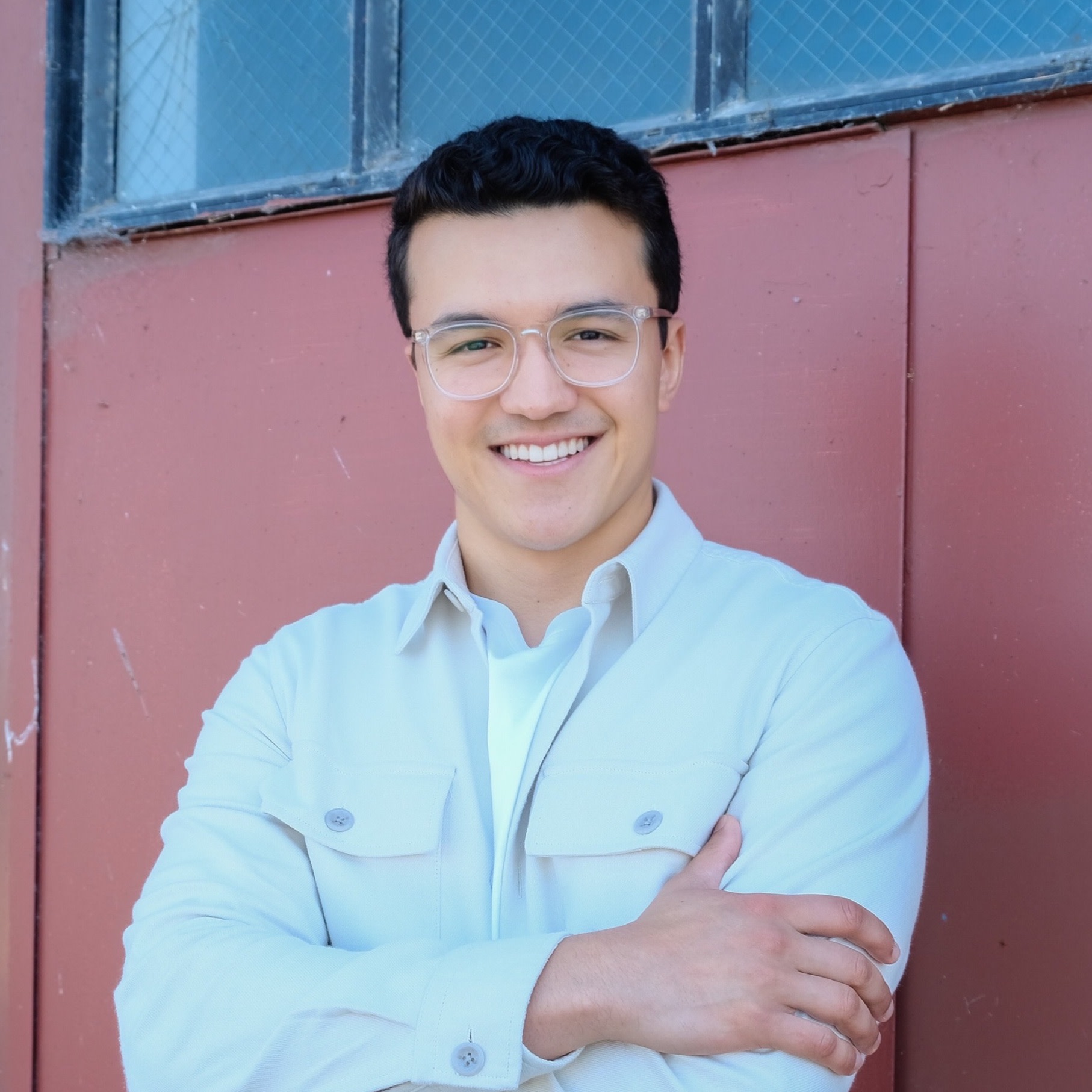
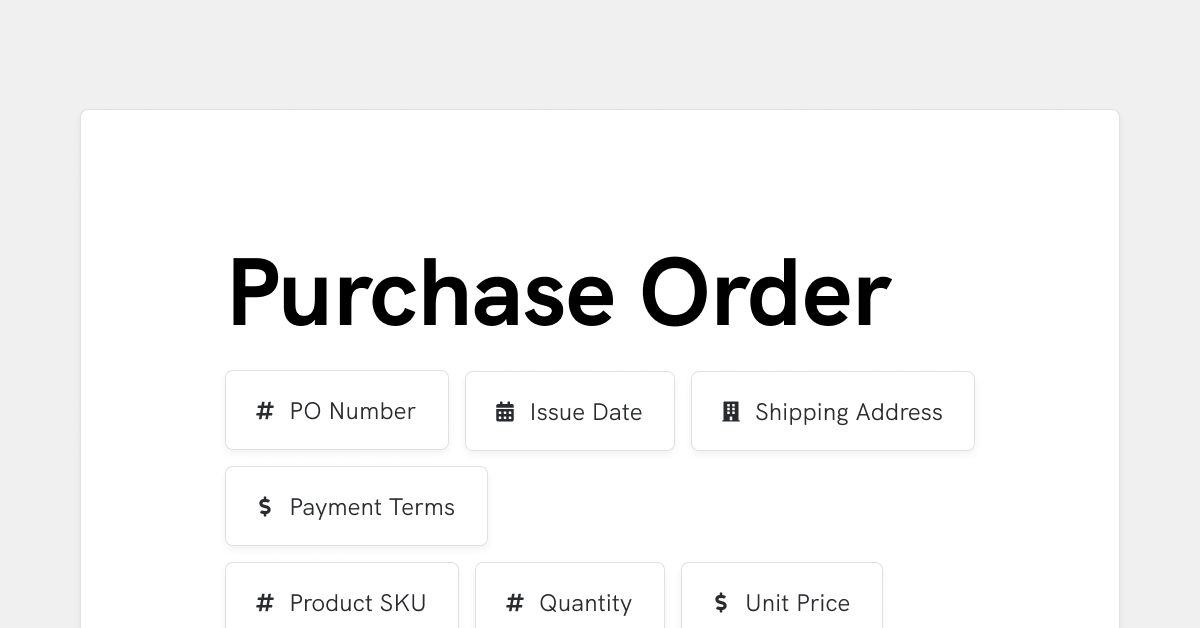
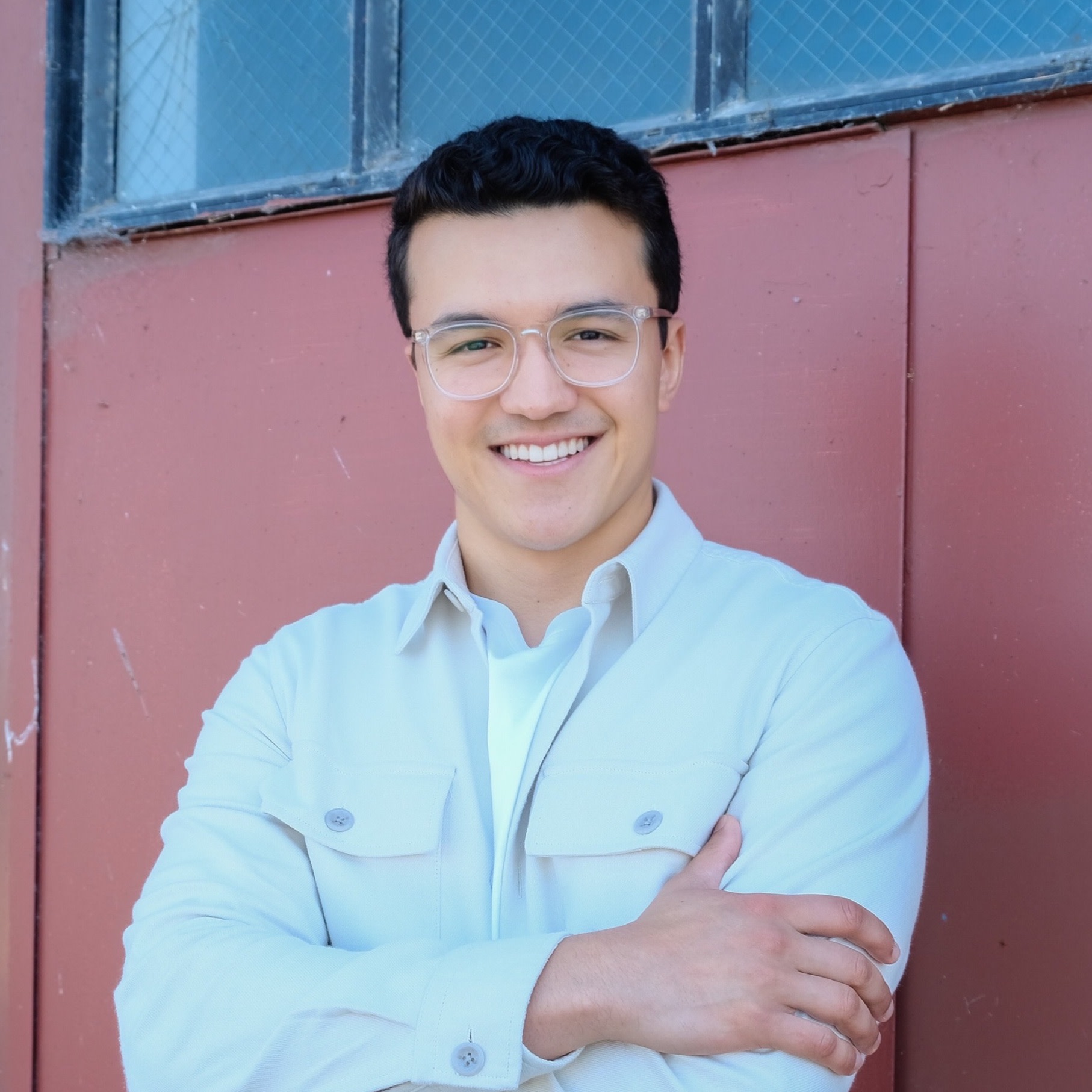
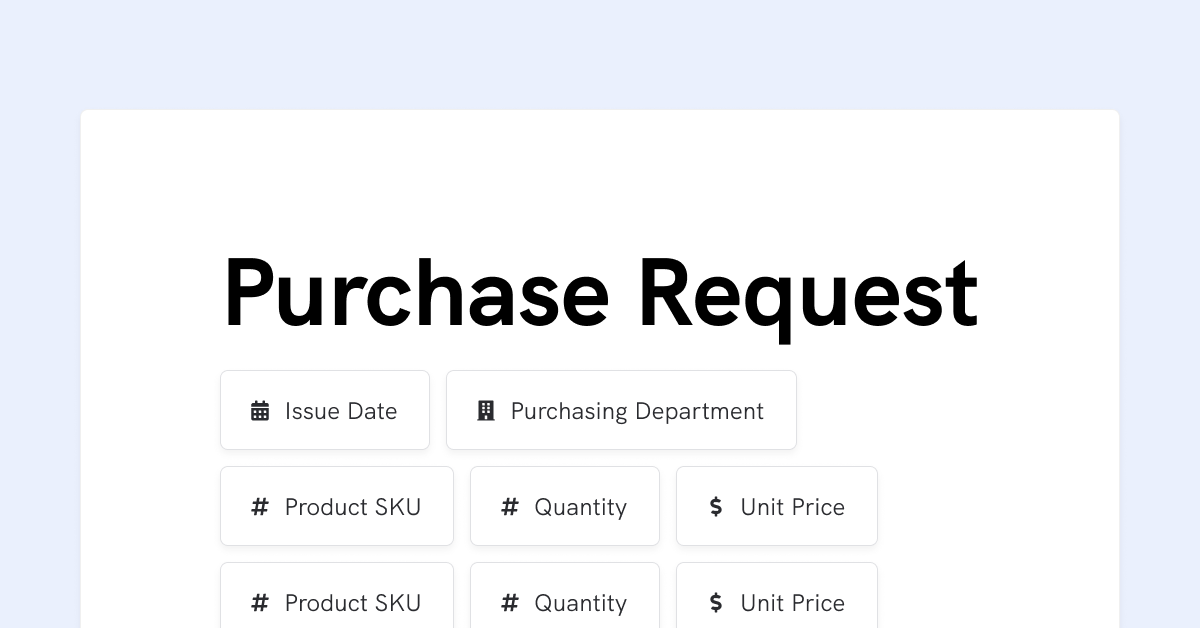
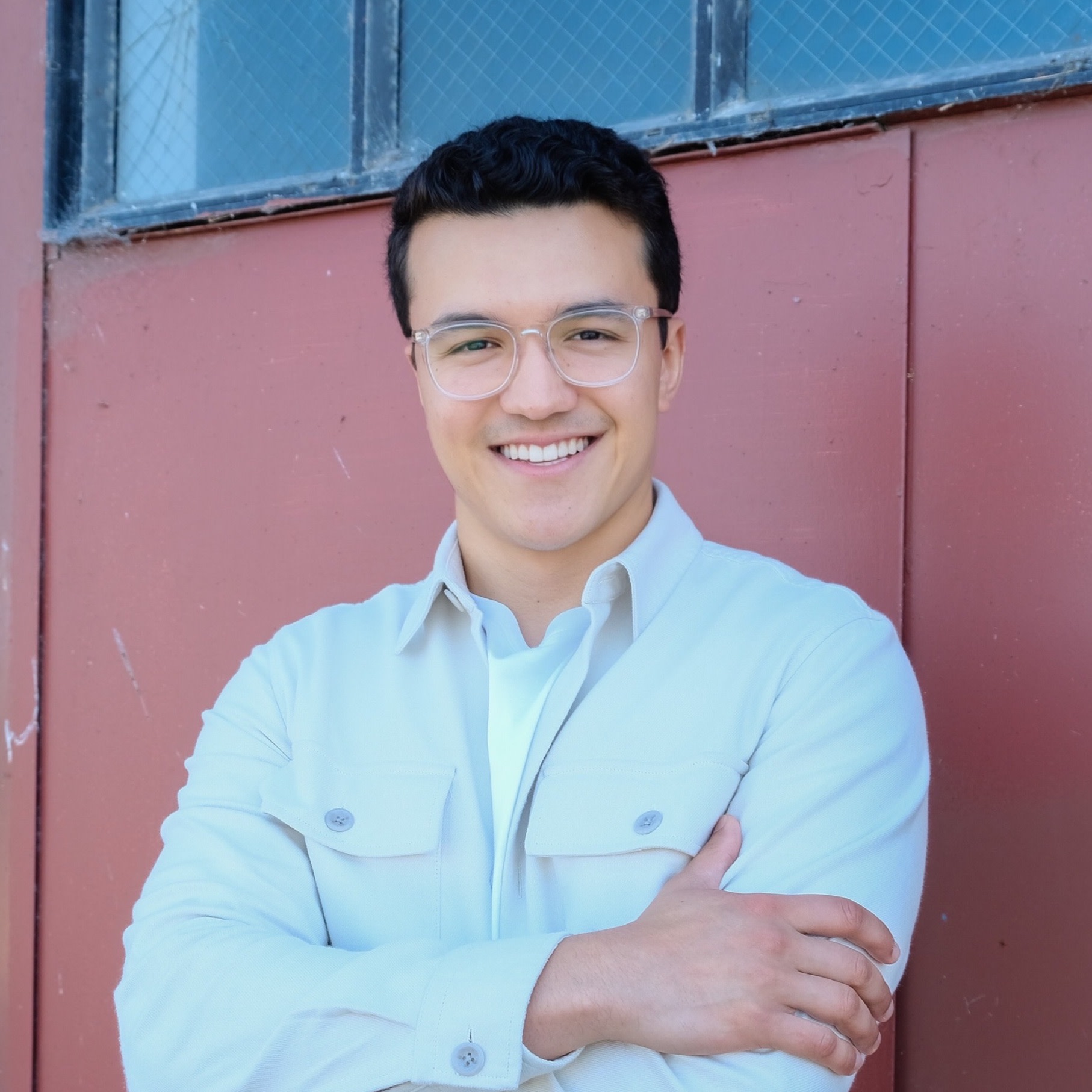
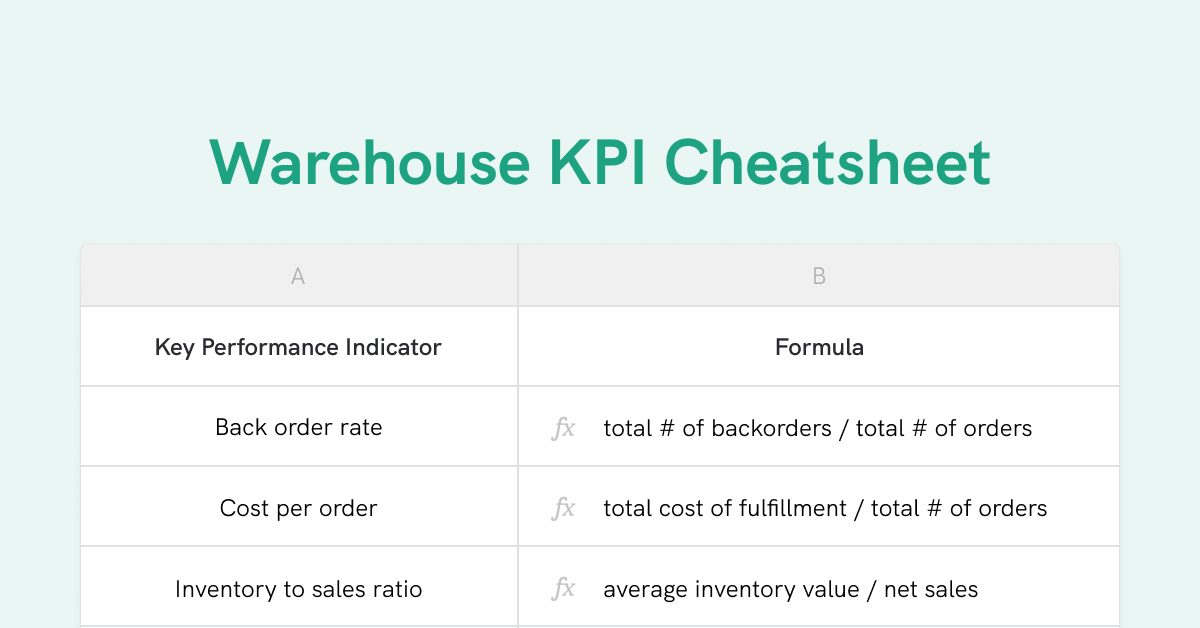
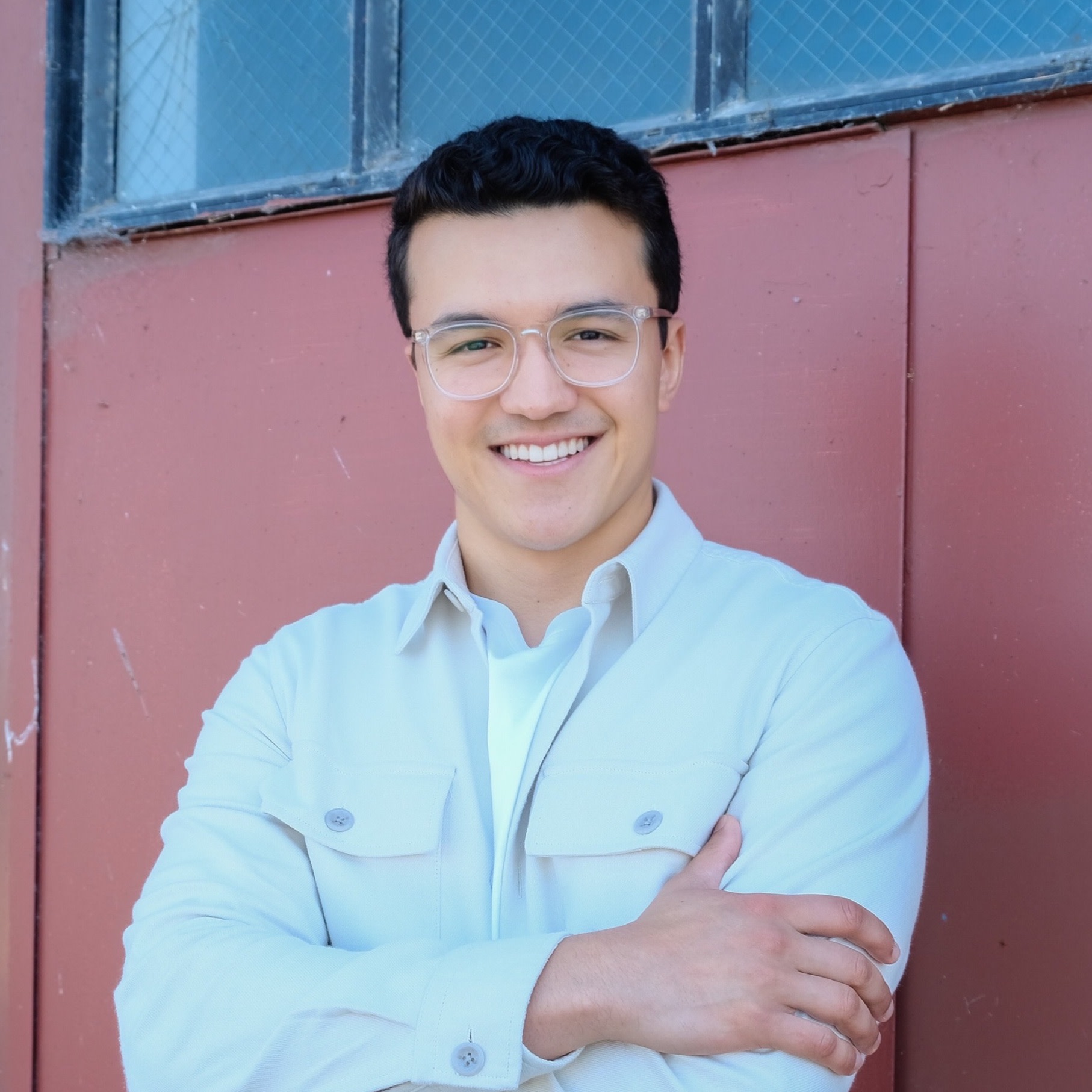